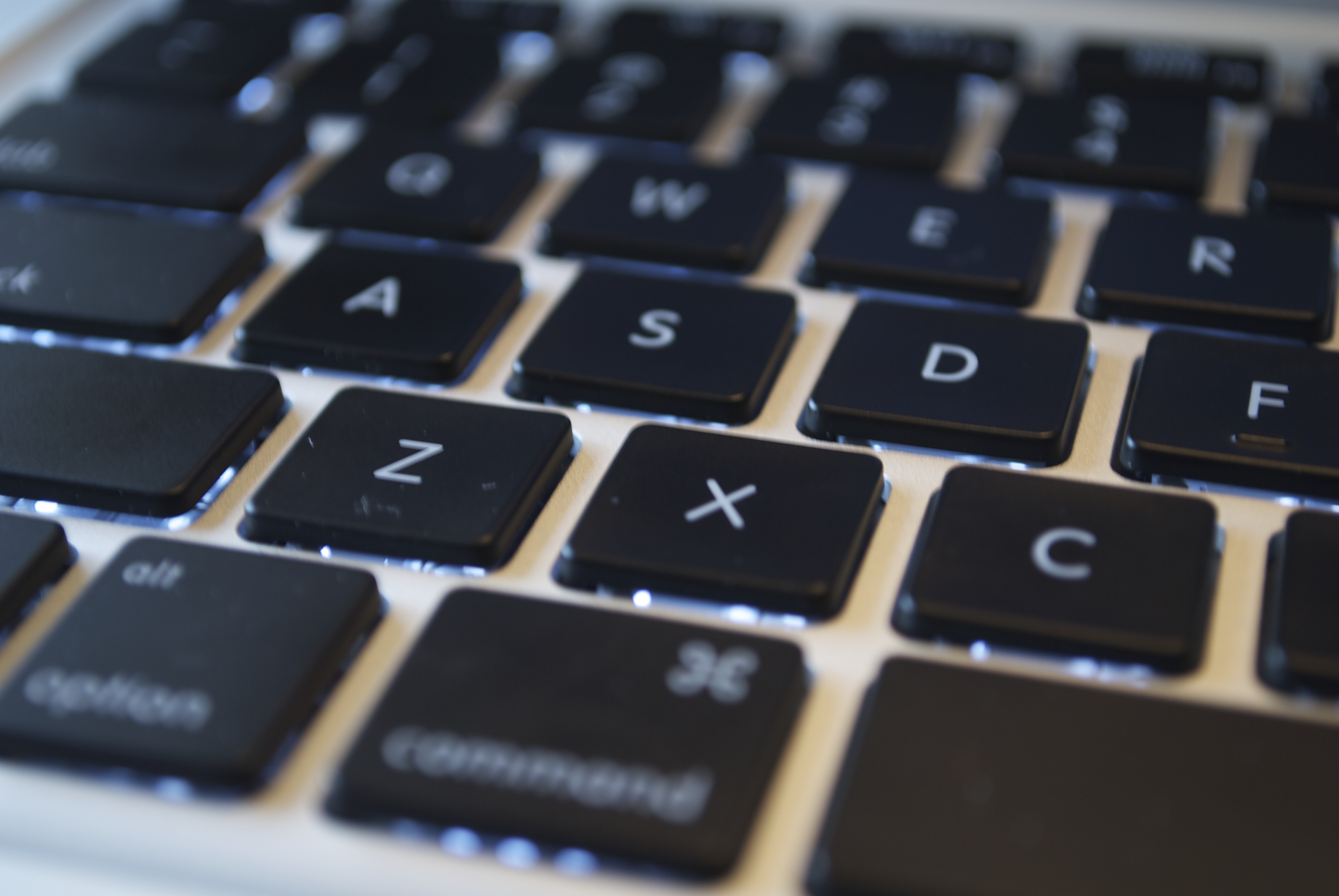
Blog
Vertical Turbine Pumps – Fear of the Unknown Part 4
Posted by: Jaime Eigner | Posted on: March 26th, 2015 | 0 Comments
“The pump has been installed and now it’s time to mount the motor and make the equipment ready for startup.”
Vertical pump motors will differ based on equipment design and options ordered. The motor will be supplied as a vertical solid shaft or vertical hollow shaft motor. Larger industrial pumps or pumps with mechanical seals are normally supplied with a solid shaft motor. Hollow shaft motors are supplied when lower horsepower is required and packing is most likely used. The motor supplied will dictate the type of drive coupling arrangement and how the pump’s impeller lift setting is adjusted.
When installing the motor, it is most important to make sure all machined surfaces are cleaned and free of any defects. Most motors will have a female fit on the motor mounting flange while the pump discharge head will have a male fit. These fits will insure positive alignment of both the pump and motor. Large motors are often supplied without mating fits, which require moving the motor to perform alignment to the pump. It is important to make sure all the correct parts have been shipped with the pump and motor. Most manufacturers ship motor equipment direct from the motor manufacturing plant.
At this time, the mechanical seal or packing should be installed prior to the installation of the pump/motor coupling. If a mechanical seal is installed, do not set it at this time. This can only be performed after the pump lift has been completed. Severe damage will occur to the mechanical seal if it is not set properly. All fittings and seal plans should be assembled and installed at this time as well. If the pump has a packing box arrangement, pack the pump per the manufacturer’s instructions. It is important to note that if the packing box is supplied with a lantern ring (seal cage), that it is located in the proper location within the packing box. This is essential for proper stuffing box operation.
Motors are equipped with oil or grease lubricated bearings. There are also times when one bearing may be grease lubricated while the other is oil lubricated. Bearings are grease packed at the factory, but oil reservoirs are shipped dry. Refer to the motor IOM for the correct lubricant to be used in the motor as well as the lubrication maintenance schedule. Remember, as mentioned in part 3, the motor bearings are required to support all the weight and down thrust of the pump rotating assembly. Now that the lubrication has been taken care of, it’s time to bump the motor to ensure the rotation of the pump is correct. Looking from the top of the motor down, the rotation of the motor shaft should be counter clockwise (CCW). If the rotation is not correct, the electrical leads must be changed to reverse rotation. If motors are equipped with a non-reverse ratchet (NRR), the ratchet will not permit the motor to turn in the wrong direction. Purchasing motors with a non-reverse ratchet is a wise investment to insure back flow through the system will not allow the pump to rotate in the wrong direction. Once proper rotation is confirmed, the motor and pump shaft are ready to be connected.
At this point, follow the installation procedures in the pump IOM for the type of coupling design supplied. The coupling arrangement supplied with the pump is designed to drive the pump as well as lift the pump rotating assembly so the impellers are set properly. These procedures and settings can be found in the manufacturer’s IOM. Once complete, it is time to set the mechanical seal or adjust the packed box. The setting procedure is based on the type of mechanical seal supplied and can be found in the seal installation instructions. If the pump is packed, leave the gland hand tight and adjust the leak rate after start up.
Once all connections are made, the shafts should be rotated to insure they turn freely with no binding. Shaft total run out (TIR) should also be taken to ensure it is within manufacturer’s tolerances.
NOTE: If shaft run out exceeds the manufacturer’s recommendations or the shaft is hard to turn or binding, do NOT start the pump. This condition indicates something has been assembled improperly, mis-machined or damaged. Investigation into the root cause and corrective actions are required.
With the shafts free turning, it is now time to start the pump. Detailed information can be found in the pump and motor manufacturer’s IOM for the proper start up procedures for the equipment. Once the pump is started, be sure any leaks are eliminated immediately and vibration levels are acceptable. If the pump has been supplied with packing, make sure some product is weeping through the packing box gland. This allows the packing to stay lubricated and cool. Do not react and over compress the packing at start up. This will cause overheating and damage the shaft. Give the pump runtime to allow the packing to seat properly. Then, adjust the packing as required until the recommended leakage is achieved.
With proper maintenance, your vertical turbine pump will supply you with many years of trouble free service.
Metro Pumps and Systems, Inc. can provide all the cradle-to-grave services you may require to specify, purchase, install, startup, maintain and when the time comes, service your vertical turbine and other pump equipment.
HAVE AN APPLICATION?
Send your request in TODAY to sales@metropumps.com for immediate attention!
About the Author
Vito Gullo has been part of the pump industry since 1976 with experience in all makes and models of pumps and rotating equipment. He has worked for major pump manufacturers as well as distribution.
He is currently the President of Metro Pumps and Systems, Inc.
Email vgullo@metropumps.com for more information.
Additional Reading: Vertical Turbine, Mixed Flow & Propeller Pumps
By: John L. Dicmas
Published By: McGraw Hill